Circular Economy
BioCellection
A chemical process to transform waste plastics into high-value industrial building blocks
Tagline
New technology to chemically break down dirty plastic bags and re-synthesize materials for advanced manufacturing
Pitch us on your solution
Today, only 9% of plastics are recycled. BioCellection is creating a market-driven solution for low-grade, unrecyclable polyethylene (PE) plastics. We are scaling an invention to chemically recycle polyethylene. We break down plastics into chemical intermediates and use them to make performance materials for cars and construction that are 20x more sustainable.
Film your elevator pitch
What is the problem you are solving?
Globally, 340 million tons of plastics are produced with an estimate to double in 15 years. Yet only 9% of plastics are recycled; the rest are landfilled, incinerated, or littered into the oceans. So little plastic gets recycled because today’s mechanical recycling cannot create valuable products from disposable packaging; single-use packaging loses 95% of its value after its first use. This is why it's cheaper to landfill plastic than to turn it into a new product. The lack of options for turning plastics back into quality products is the reason that there are no scrap markets for major plastics like polyethylene (PE) despite consumers putting them into a recycling bin.
We realized that the key to preventing plastic pollution is to create markets for waste plastics so that it will become a raw resource that is profitable to keep out of the oceans, just like cardboard and metals. This could only be enabled through a new technological innovation that can turn currently unrecyclable plastics into truly valuable products. Another reason to work toward a circular economy is the significant amount of carbon reduction we can achieve through making new materials out of waste, as opposed to extracting virgin supply.
Who are you serving?
Waste generators/ processors: MRFs and Construction companies are seeking an outlet for their PE plastics. All markets on the west coast have crashed since the China plastics ban. They are willing to pay to have the plastics be recycled by us instead of pay to landfill.
Chemical buyers: we sell them base chemicals that are the same as those they get from virgin oil in quality and price. They get to increase their supply security and increase their portfolio sustainability.
What is your solution?
BioCellection is tackling the plastic challenge by creating a novel way to recycle polyethylene (PE), which is the top produced plastic produced at 150 million tons per year. PE is commonly used in disposable applications such plastic bags, sheets and bubble wrap, agricultural plastics, containers. Our technology turns PE waste from city waste management plants into valuable chemicals called dibasic acids and then we use these chemicals to make durable materials for the automotive, construction, and electronics industries.
Our impact is threefold: 1) prevent pollution by using plastic as a resource to make valuable products, 2) fight climate change by reducing carbon emissions that would otherwise be made in the chemical production process, 3) create a market-driven solution in developing countries by paying wastepickers to do cleanups. Our vision is preventing over 150 million tonnes per year of PE plastic from becoming pollution, and saving 3 billion tonnes of CO2 per year from being released in chemical production. It is also important to note that these impacts can be made without changing the supply chains of how the chemicals and derivative materials are used, making fast adoption achievable.
Select only the most relevant.
Where is your solution team headquartered?
Menlo Park, CA, USAOur solution's stage of development:
PilotSelect one of the below:
New technologyDescribe what makes your solution innovative.
Today, low density PE (LDPE) waste is used in all flexible packaging. However, it is not recyclable mechanically and can only be chemically recycled into fuels: naphtha, crude oil, diesel, syngas -- all of which contribute to emissions because in the USA, plastics are not produced from oil but from natural gas. Therefore, plastic-to-fuel is not a circular technology.
Our solution has the following innovative elements:
- a new process invention to sustainably recycle PE waste by oxidizing it into chemical intermediates dicarboxylic acids
- creates new applications for these chemical intermediates in performance materials nylons and polyurethanes
- formulation innovation in the nylons and polyurethanes
- system design innovation for the equipment to carry out the new chemical process invention
In our lab, we have created step-by-step the entire process to take a piece of dirty PE plastic from the waste plant, turn it into chemical intermediates, and now we are turning that into nylons and polyurethanes.
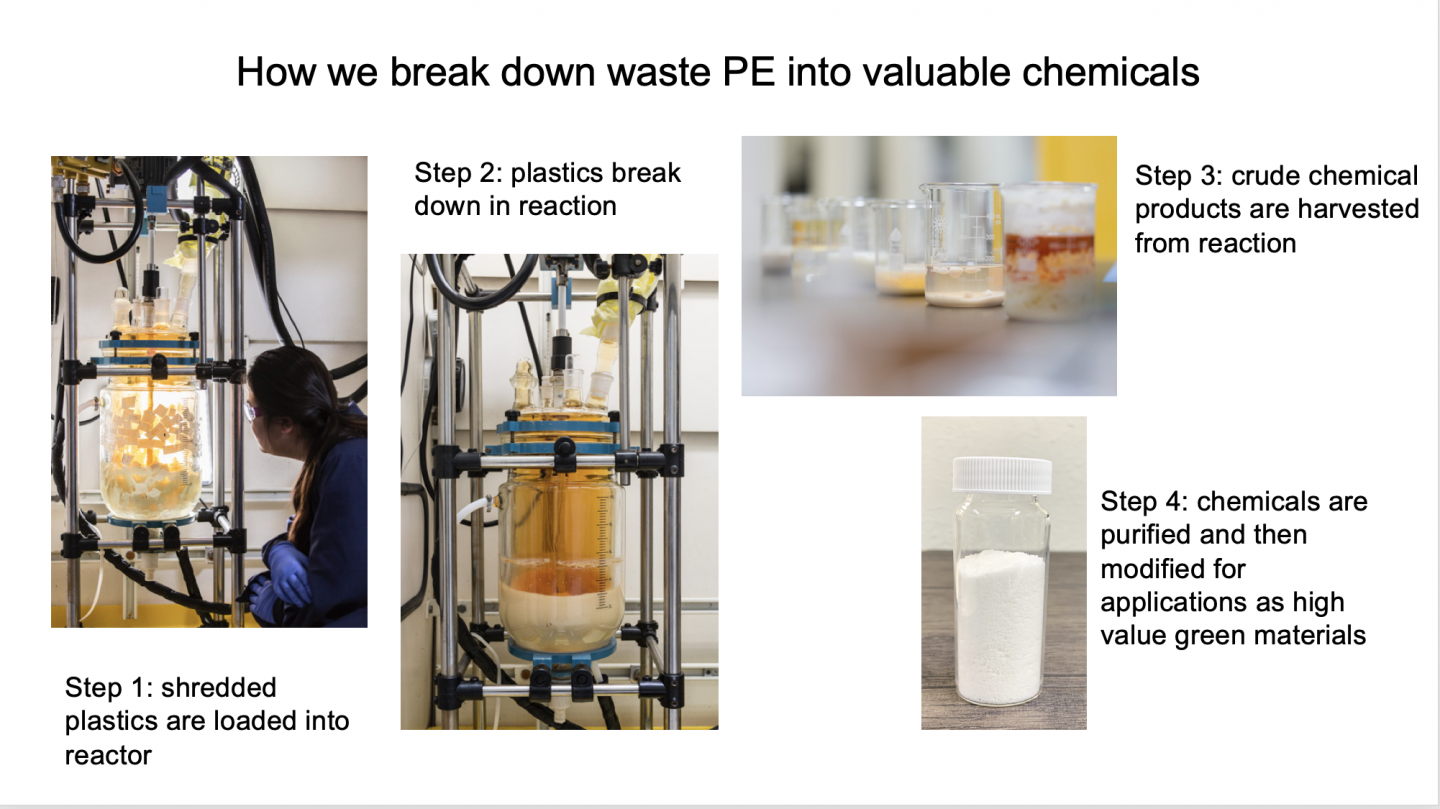
First nylon material synthesized with virgin-quality chemical intermediates made by recycling PE waste!
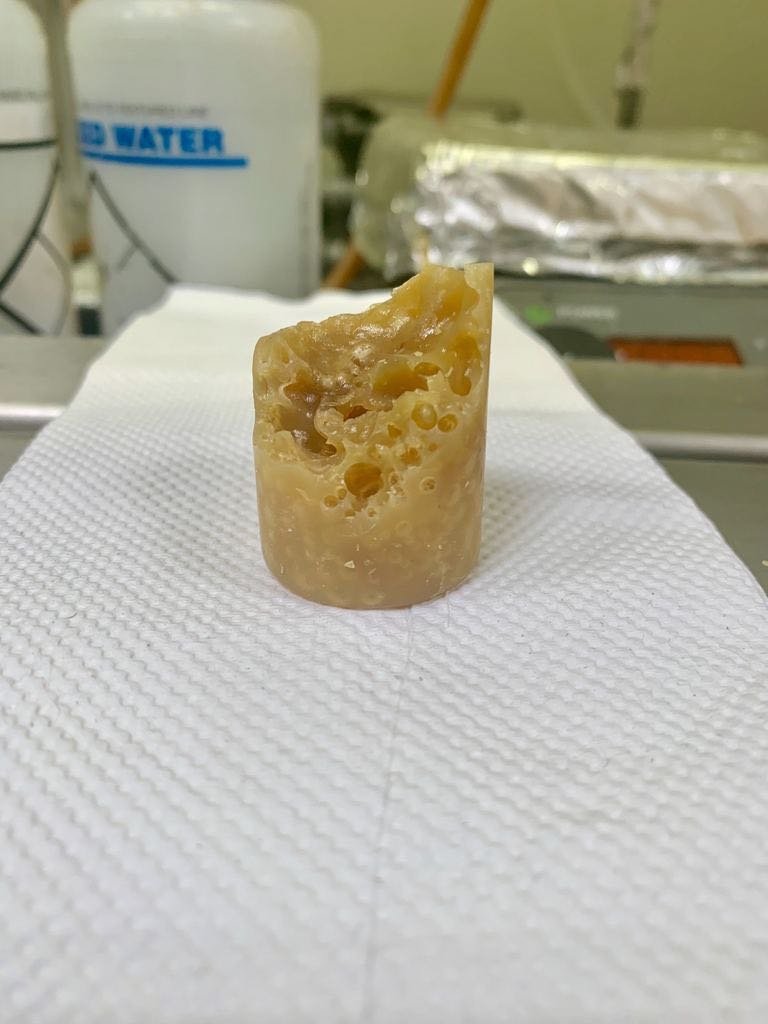
Our ambition is to become the next BASF powered on PE waste as the carbon feedstock.
Commercially, this technology will operate as chemical plants where metropolitan plastic waste will be centralized and processed. Here is what the commercial chemical process system design could look like:
Describe the core technology that your solution utilizes.
BioCellection’s patent-pending technology is a novel, proprietary chemical recycling process that:
- first breaks down polyethylene (PE) plastic waste into chemical intermediates via selective chemical oxidation, and
- then re-synthesizes intermediates into high-value and proprietary performance materials nylon and polyurethane.
1. Contaminated, unrecyclable polyethylene (such as bags and shrink wrap) are shredded.
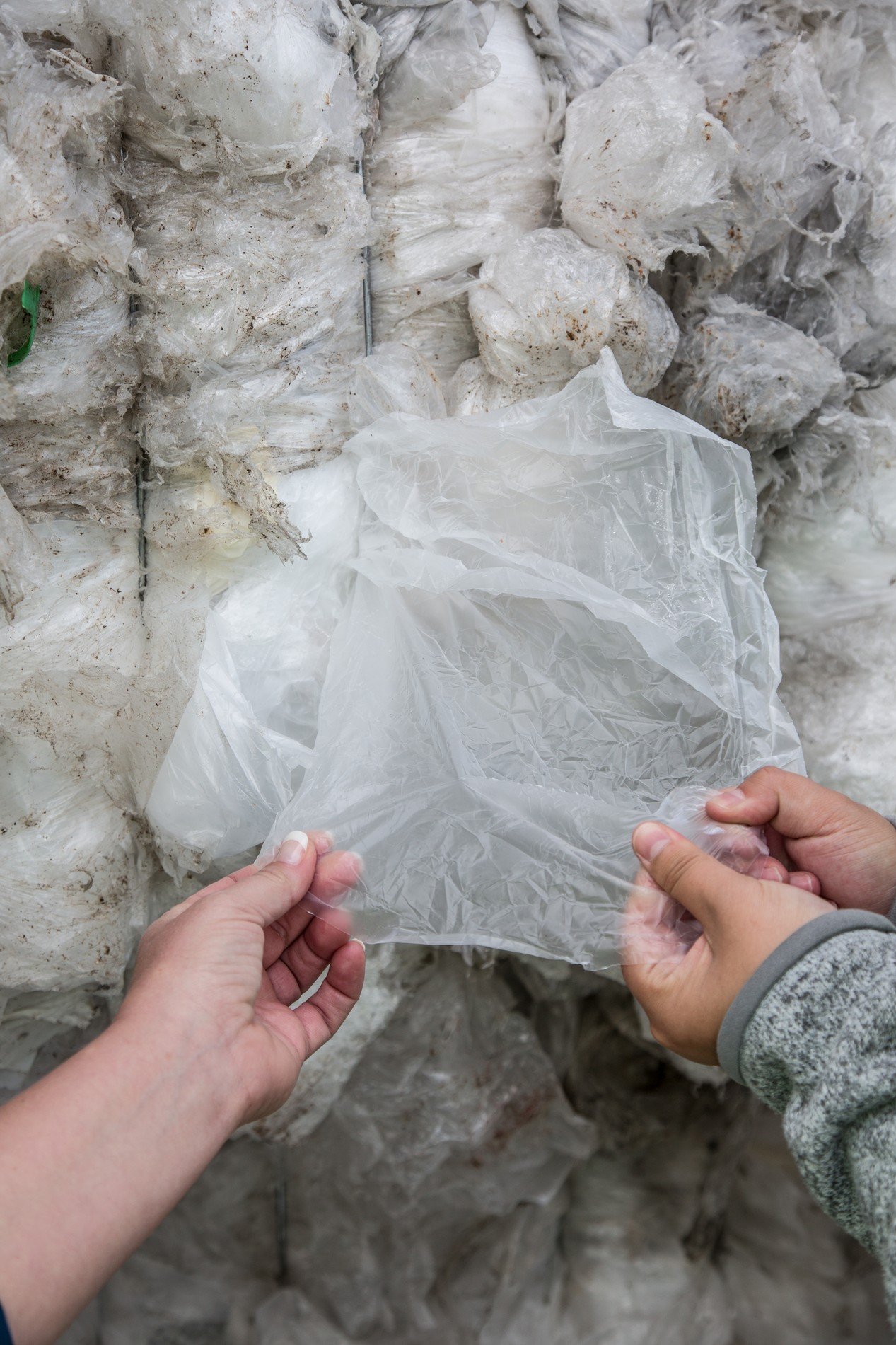
2. A low-heat chemical reaction takes place where a proprietary oxidant is added.
In 3-9 hours, the PE polymers with hundreds of thousands of carbons are chemically broken down into product compounds with 4-10 carbons. These compounds are purified in multiple steps and the oxidant is recycled.
2. The harvested compounds are then used to make engineering plastics --novel nylons and polyurethanes, which are important materials for advanced manufacturing in automotive and electronic parts, insulation, coatings, apparels, and more. Today, such materials are produced mostly from fossil fuels.
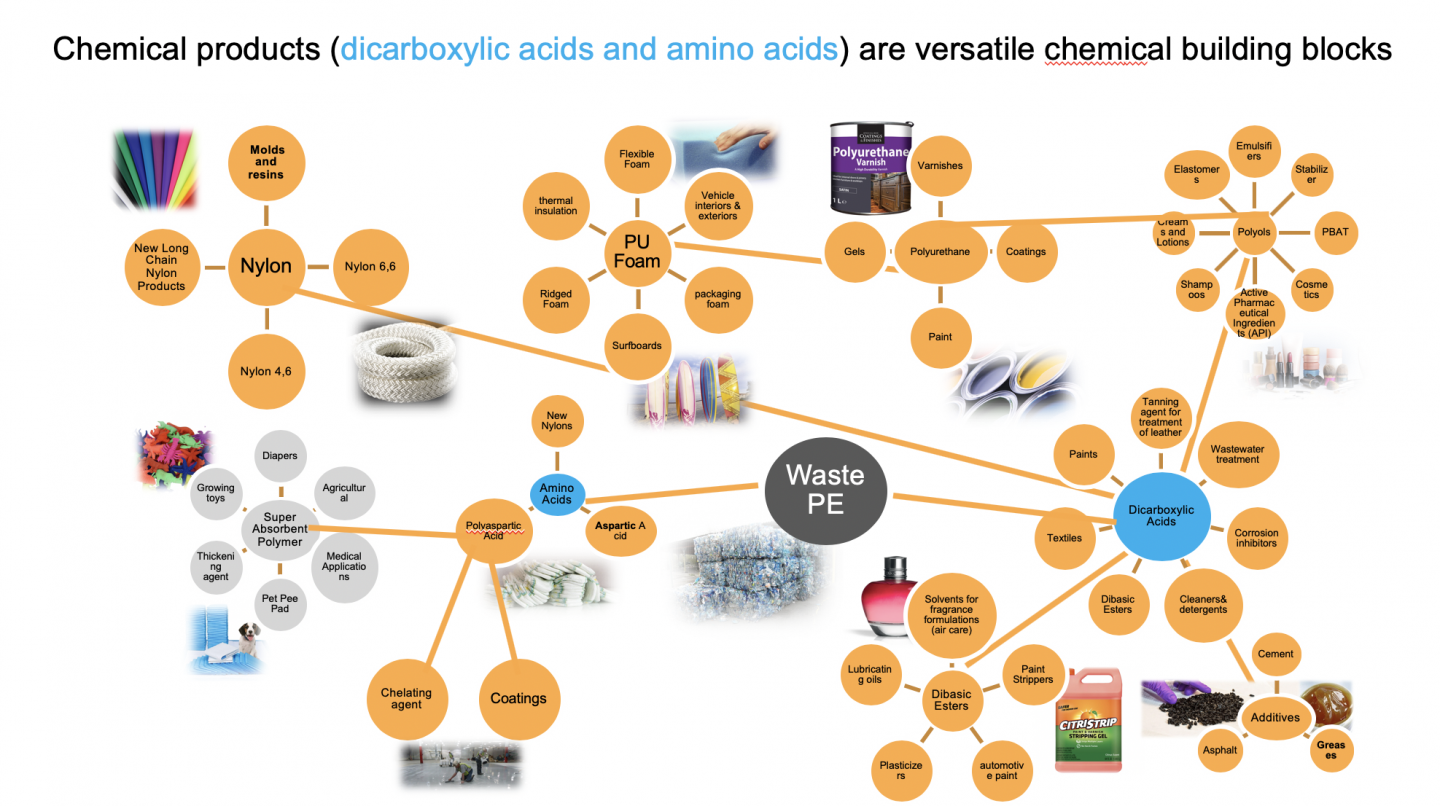
Our technology creates plastic circularity by turning low-value packaging waste into high-value performance materials that stay in the economy longer and prevent carbon emissions associated with their traditional production from fossil fuels.
Please select the technologies currently used in your solution:
Why do you expect your solution to address the problem?
Activity: a team of scientists, engineers, entrepreneurs works together to invent a new way to recycle LDPE waste and turn it into valuable chemical intermediates and performance materials.
Outputs:
- new process inventions are created to break down LDPE into various different kinds of chemicals
- new products are developed using these circular chemicals
- scale-up models and economics are completed to turn this process invention into a manufacturing-scale solution
Short-term Outcomes:
- City of San Jose and local stakeholders including waste management plant GreenWaste Recovery and construction firm HDC who has lots of LDPE waste from construction sites signed up for $240k paid pilots for our startup to break down their LDPE waste
- chemicals are sent to potential partner companies (Unilever, International Flavors and Fragrances) for co-development on non-materials applications in the homecare (fragrances) space
- new products made by the team are tested with compounders and manufacturers in additive manufacturing and injection molding. Application fits for these new materials are identified
Long-term Outcomes:
- understanding of the demand for these chemicals and downstream derivative products (fragrances and performance materials) inform scale-up capacity
- circular manufacturing facilities are built and operated to turn PE waste into circular products
- cities, waste plants, and construction firms establish a pipeline with our facilities to send their LDPE waste to us instead of to landfill/ export
- circular products made through our innovation become components in consumer products that are sold to everyone through partner brands
- LDPE gains recycling markets and ceases to become waste
- sustainable products made from upcycling LDPE is made available to the world!
We close the loop on LDPE!
Select the key characteristics of the population your solution serves.
In which countries do you currently operate?
In which countries will you be operating within the next year?
How many people are you currently serving with your solution? How many will you be serving in one year? How about in five years?
Even at the current lab scale (processing 0.5-1kg plastic/day), we are receiving plastic waste from waste management companies and construction firms and are being paid for providing a PE plastic recycling service. We have a contract with the Google campus construction company HDC as well as a pilot partnership with the City of San Jose and GreenWaste Recovery. Thus, we are serving various teams and departments in these entities - approximately 100 people.
In a year, we will be rolling out our demonstration unit (will process 50-100kg plastic/day). This recycling capacity is equivalent to 1% of San Jose’s plastic film waste, which means we will be serving roughly 1% of San Jose households - approximately 10,000 people. At this stage, we may be pre-selling the material products to a handful of early buyers.
In 5 years, we will be starting to operate our first industrial/commercial facility (will process 5-10 metric tons plastic/day). This recycling capacity will be able to fully serve a large city with a population of approximately 1,000,000 people. We will also be selling the material products at commercial scale, potentially serving 5,000,000 more customers. That brings our total impact to 6,000,000 people that year.
What are your goals within the next year and within the next five years?
Within 1 year: our goals are product development, early sales, and process scale-up - we must succeed in all 3 arenas to demonstrate business economics and have the opportunity to further scale in the upcoming years.
Rest of 2019:
Develop first qualified product (make nylon and polyurethane and then best material to launch)
Launch our first product into the market
Rebrand the company and develop communication strategies toward different stakeholders and the general public
2020:
Complete detailed process engineering and budget for the demonstration unit
Raise our Series A financing
Secure and renovate new facility and obtain relevant permits
Complete construction and installation of the demonstration unit
Within 5 years: our top goals are business and growth strategies, expanded sales, infrastructure funding, and operations scale-up - we must be commercially viable to deliver this technology’s potential impact on the environment and the economy.
2021:
Operate the demonstration unit to collect data for designing an industrial plant
Obtain more contracts/partnerships with waste generators
Produce material products for more customer testing
Sell to small buyers and sign pilot deals with large buyers
2022:
Conclude demonstration with comprehensive process performance data and scale up plan
Raise Series B
Identify an industrial partner and collaborate to scale up to the first industrial facility
Complete detailed process engineering for the facility
2023:
Construct the facility
Expand operations (channels and logistics) and increase pre-selling for large volumes
2024:
Complete construction
Start commercial operations!
What are the barriers that currently exist for you to accomplish your goals for the next year and for the next five years?
The following barriers are relevant to both the demo unit scale up (within 1 year) and the industrial scale up (with 5 years).
(regulations) Permitting/facility preparation: A substantial amount of time is required to obtain permits and order equipment for any chemical scaleup project.
(technical) Scaleup: When a chemical process is scaled up, numerous components need to be modified. There is inevitably a level of trial and error when operating the process in much larger equipment.
(operations) Sample generation: Introducing new products requires iterative test cycles and some pre-scale-up capabilities to create samples for potential customers before we can start production to fulfill the actual purchase orders.
How are you planning to overcome these barriers?
Demo (1 year)
Industrial (5 years)
(regulations) Permitting/facility preparation:
Demo: Our early engagement with San Jose City's planning and construction departments, various environmental agencies (air quality and sewage management districts), as well as Engineering, Procurement and Construction (EPC) firms will expedite this. We also have a great relationship with the San Jose mayor.
Industrial: We will identify a strategic scale-up partner with experience in establishing chemical plants or has an existing site with relevant permits and infrastructure that we can build from.
(technical) Scaleup:
Demo: We will work with a professional engineering team at one of two EPC firms we’ve engaged with as well as an in-house process engineer to produce the most flexible design for the equipment to enable potential alterations. For additional support, we have access to two other process consultants who have previously helped us.
Industrial: We will continue working with the selected EPC firm (they specialize in making commercial scale equipment) that has designed and built our demo. At this time, we will also have a team of in-house engineers and can consult our scale-up partner who must know a lot of best practices.
(operations) Sample generation:
Demo: Various toll manufacturers can generate samples once we provide a standard operating protocol. These projects typically cost $3-8K per day. A 2-week project can fulfil a large number of sample requests before the demo is ready.
Industrial: Before the plant is operational, we can run short projects in the existing demo equipment to fulfil sample requests.
If you have additional video, provide a YouTube or Vimeo link to your video here:
Select an option below:
For-ProfitIf you selected Other, please explain here.
N/A
How many people work on your solution team?
- Miranda Wang, Cofounder & CEO (FT) - UPenn alum
- Jeanny Yao, Cofounder & COO (FT) - UToronto alum
- Dr. Jennifer Le Roy, Director of R&D (FT) - ex-Oxford PI
- Dr. Tapaswy Muppaneni, Chemical Engineer (FT) - process early co-inventor
- Dr. Thomas Burgoyne, Analytical Chemist (FT)
- Dr. Katrina Knauer, Polymer Scientist (FT) - ex-BASF senior polymer scientist
- Dr. Russell Pratt, Organic Chemist (FT) - Stanford PhD with startup exit
- Reese Griffith, Business Development Associate (FT) - entrepreneur with 4 small business exits
- David Pilsk, Laboratory Assistant (FT)
- Vincent Zollo Jr, Laboratory Assistant (FT) - UMiami PhD candidate
- Teeba Al Ramah, Operations Associate (FT)
- Rick Eastman, External Controller (PT)
For how many years have you been working on your solution?
8
Why are you and your team best-placed to deliver this solution?
External reasons:
- awareness for the plastic problem is higher than ever
- people are starting to understand why our approach makes sense (entering hockey stick curve) - can build momentum better now
- China plastic ban in 2018 created very favorable market conditions for us
- industry is beginning to make real investments in sustainable sourcing - creating demand for our products
Internal reasons:
- Cross functional team with all bases covered to meet the challenge (different overlapping and relevant knowledge areas in synthetic chemistry, polymers, analytical chemistry, chemical engineering, sales and customer service, fundraising and PR, operations and hiring)
- well-established company foundations enabling efficient operations and a long-term view to the solution
- sufficient funding for goals in next 15 months
- mission-aligned
- smart and connected investors who can help recruit resources and provide sound advice
With what organizations are you currently partnering, if any? How are you working with them?
BioCellection has 6 groups of partners:
- City governments: City of San José Environmental Services Department - the City has contributed $120k funding and access to the waste industry to direct us to the correct plastic waste to develop recycling for.
- Waste management companies: GreenWaste Recovery - to increase zero waste metrics, GreenWaste partners with us to ensure we have access to waste supply for our pilots and future scale-up. Press release of our current partnership: http://files.constantcontact.c...
- Construction companies: HDC - pays BioCellection $450/ton to recycle their LDPE and HDPE waste collected at the Mountain View construction sites
- Specialty chemical companies: International Flavors and Fragrances - co-development partner/ JDA to use our sustainable chemical supply to make fragrances for air fresheners
- Brands in homecare space - SC Johnson and Unilever - direct co-development/JDA on surfactant compounds made from our chemicals, and adopting chemicals made by IFF in formulations
- Additive manufacturing companies: Essentium - testing our newly formulated nylons on their 3D printing platform for customers in the small-batch manufacturing space
- Scale-up:
Therma Corp - to design the controls for the demo unit.
De Dietrich Process Systems and Pfaudler - preliminary engineering of the demo unit
Lee Enterprises - developing and refining process economics.
What is your business model?
We sell a recycling service to large volume waste generators (cities and their waste plants/material recovery facilities, construction companies) at $50-$450/ton. We create value by providing an alternative to landfilling. We have signed one deal with HDC (Google’s construction company) to process their PE sheets for $470/tonne.
We sell chemicals to specialty chemicals and fragrance companies like International Flavors and Fragrances at market prices $1,600-$21,000 per tonne. Our costs to produce chemicals is $2,500/kg. We create value by providing a sustainable chemical supply that is virgin-grade with a differentiated composition that can lead to new and exciting products.
We sell advanced engineering plastics (nylons, polyurethanes, and future biodegradable products) formulated with our chemicals by vertically integrating one step further. Prices are $20-70/kg. We sell through partnerships with 3D printing companies like Essentium (people can buy spools of our nylon online). (hypothesis) We create value by creating a product with a low melting point and good tensile strength, suitable for making materials for light weighting hardware like rockets, airplanes, and solar panels.
1000kg = 1 tonne
What is your path to financial sustainability?
Scale-up steps:
Lab scale: 1kg/ day - we have raised enough money to advance through this stage
Demo scale: 100kg/day - we need to raise $7.5M in March 2019. Options are debt financing from impact investors/ PRIs.Potential blend of super angel investment.
Reference scale: 3-10 tons/day (profitable) - $20M in 2021. Options are infrastructural grants and low-interest loans. Potential blend of VC.
Commercial scale: 10 tons/day + (profitable) - grants & debt, revenues.
One strategy we're assessing is to work with manufacturing partners with existing infrastructure to scale from demo to reference.
Why are you applying to Solve?
We are seeking commercialization opportunities for the products we are making from our technology platform. The following kinds of companies are good examples of partners for us:
- auto companies (try our nylons)
- furniture companies (try our polyurethane foams for cushions)
- homecare companies (try our chemicals)
- 3D printing company with ability to test and give us feedback about the polymers we're inventing
What types of connections and partnerships would be most catalytic for your solution?
With what organizations would you like to partner, and how would you like to partner with them?
HP - we'd like to explore applications in 3D with our circular nylons and thermoplastic polyurethanes.
Esquel Group - we'd like to use your poly bags, Margie! Maybe we can make buttons with the nylons or foams for a product line.
Brands and manufacturers that can test and adopt the chemicals or derivative materials.
If you would like to apply for the GM Prize on Circular Economy, describe how you and your team will utilize the prize to advance your solution.
We fit the criteria for this prize because:
- we have created a way to take unrecyclable waste and upcycle it into valuable and useful performance materials in a way that cuts 20 MT CO2 emissions/MT
- we believe our nylons could be applied in GM's cars. Each kg nylon is made from recycling 0.5kg of previously unrecyclable PE waste!
If you would like to apply for the Innovation for Women Prize, describe how you and your team will utilize the prize to advance your solution.
In the second batch of products we formulate from our chemical intermediates, we will work on a super absorbent polymer (similar to polyaspartic acid), which can be used to make biodegradable sanitary napkins. The impact of this project is to 1) recycle currently unrecyclable plastics in developing countries, and 2) make available safer and more biodegradable feminine hygiene products. We will use this prize to fund this product development.
Solution Team
-
Miranda Wang Co-Founder and CEO, BioCellection Inc
to Top
Our Solution
BioCellection